

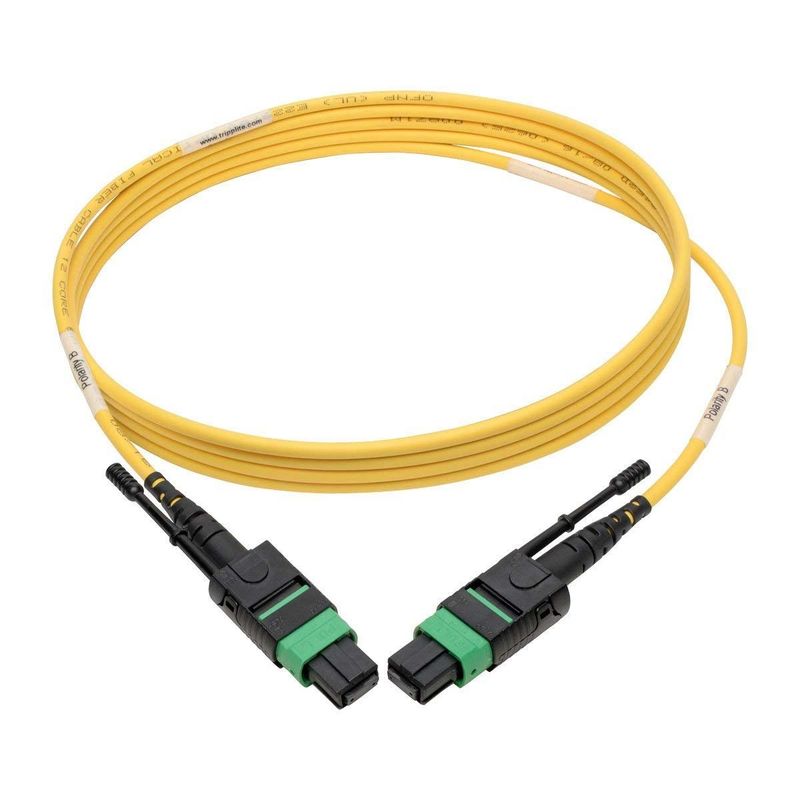
For MPO connectors, there is greater variation among the procedures used by different assembly manufacturers.Īll MT-ferrule polishing processes have three main objectives:Ī. The ceramic materials used for cylindrical ferrules are more uniform among vendors, and identical or very similar polishing processes can be used for cylindrical-ferrule connectors from different vendors. At least three of the vendors use a variant of polyphenylene sulfide (PPS), a thermoplastic polymer. The polymers’ properties have a bearing on the polishing procedures. Several vendors offer MT ferrules, and they use different polymers. In short, all challenges and difficulties in achieving good terminations are multiplied for MPO connectors. Achieving low-loss connections for multiple fibers in one mated pair is much more complicated than with single-fiber connections, further reinforcing the need to carefully follow well-established procedures to minimize quality and yield problems. The main differences are in polishing: materials required the number of steps involved and the industry-defined finished geometries of the polished end-face. The presence of multiple fibers and the polymer ferrule material mean that the assembly-production processes are substantially different from those used with traditional single-fiber ceramic or metal ferrules. Multi-mode applications typically require “flat” (non-angled) ferrule end-faces. Singlemode ferrules can be purchased as “flat” (where the cable-assembly producer will need to polish the 8-degree angle into the ferrule), or as “pre-angled”, with the 8-degree angle already generated (which reduces polishing time). MT ferrules and MPO connectors are available for both single-mode and multimode fibers, with the only difference being tighter dimensional tolerances on the Singlemode versions. Single-mode applications typically require a 8-degree polished MT end-face. Another example is a 32-hole product that has two rows of 16 holes i The current most commonly-used configurations are 12-hole (1 row of 12) or 24-hole (2 rows of 12). For example, a 72-hole version on the market has six rows of 12 holes. The number of holes in a single row can range from 4 to 16, and there can be up to six rows in one ferrule. Thus, one mated pair can provide connector joints for up to 72 fibers. The options in MT ferrules / MPO connectors from several companies cover a range from 4 to 72 holes per ferrule. How many holes? The answer will depend on what equipment and protocols are being used in the fiber network. Mated-ferrule alignment is achieved with two guide pin holes molded into the MT ferrule itself. The fiber hole spacing (“pitch”) of MT ferrules is standardized to ensure alignment with a mating ferrule. An MT ferrule is a rectangular polymer (plastic) block with holes for multiple fibers, where typical single-fiber ferrules are ceramic, requiring different polishing processes and materials. What are the differences between MT ferrules and standard connector ferrules? Unlike cylindrical ferrules which are typically for connecting single fibers, MT ferrules are designed to mate multiple fibers, greatly increasing the number of fibers that can be mated per-connection. In this article, we focus on the special products needed to polish polymer ferrules in MPO-type connectors. In Part 2, we covered films for polishing zirconia ferrules. In Part 1 of this series, we covered the use of films with pressure-sensitive adhesives. MT ferrules require different polishing procedures
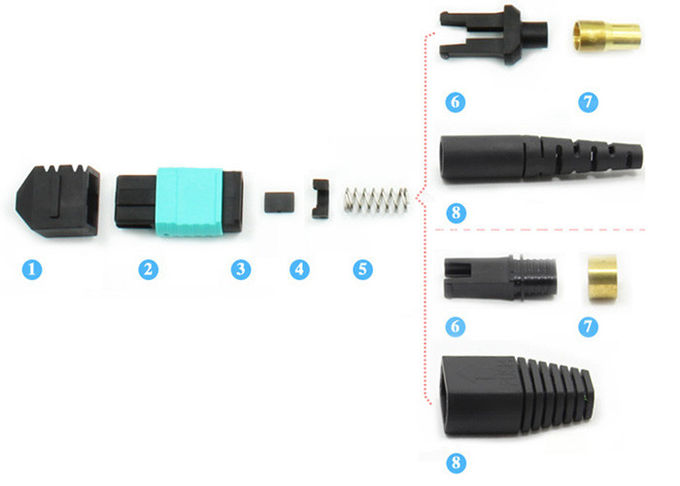
Syringes, Tips, Pistons and Barrels, Plunger.
